What is Six Sigma?
“Six Sigma is a quality program that, when all is said and done, improves your customer’s experience, lowers your costs, and builds better leaders”. — Jack Welch
Yes, what actually is Six Sigma? Before handing you the exact answer to this question, it must be said this article will focus on two sides of this methodology. Because looking at the statistical and project-based aspects will lead to an answer to the question, that has been given much thought:
What is Six Sigma?
The project-based side of Six Sigma
‘Six Sigma’ is a well-known concept, which as a matter of fact goes by many different names. ‘Operational Excellence’, ‘Zero Defects’, ‘Customer Perfection’ or ‘Customer Excellence’ are examples of such. However, each of these names define the same concept: a benchmark for quality which strives after perfection. Six Sigma eliminates defects and variations in every process – fabrication to facturation and production to service – by using a data-driven approach.
This methodology has one main focus: the implementation of a strategy based upon measurements, focusing on process improvement and the limitation of variation by applying these process improvements. By applying two Six Sigma sub-methodologies, this can be achieved. The process of Define, Measure, Analyse, Improve and Control – also known as DMAIC – is a methodology focusing on possible improvements within already existing processes, by searching for incremental improvement possibilities while keeping an eye on specification requirements. The other sub-methodology is called DMADV, which stands for Define, Measure, Analyse, Design and Verify. This improvement system is used to develop new processes or products with the quality of Six Sigma. Though, it can be used if an existing process needs more than ‘simple improvement’ as well.
Both of these systems are executed by Green Belts, Black Belts and under the supervision of Champion Belts.
Why implement the use of Six Sigma?
One example of why the implementation of Six Sigma leads to good things, is the company General Electric. They first used this methodology after Motorola and Allied Signal in 1995. And their profit over the first five years is estimated to be $10 billion. They have become one of the most successful companies who appeared to have implemented Six Sigma. This led to other companies discovering what Six Sigma could actually mean for their business.
The statistical side of Six Sigma
We can talk about ‘implementing Six Sigma’ all we want, but what does it mean? As stated before, it is a benchmark for quality which strives after perfection. However, the quality as known by the customer does not cover all statistical implications. Six Sigma is a methodology, originated from maths and statistics.
Six Sigma quality focuses on decreasing the variation in the output of processes. This will make sure the customers’ experience concerning processes will statistically result in less than 3,4 defect parts per million (ppm) chances in the long term. A process with just one specification limit then results in six standard deviations between the process’ average and the customers’ specification limit. Where do you think the name Six Sigma comes from?!
A process with two specification limits contains a little more than six standard deviations between the average and the limit, resulting in a defect-percentage which corresponds with the equivalent of the six deviations. USL stands for Upper Specification Limit and resembles the upper customers’ wish. Logically, LSL means Lower Specification Limit, which stands for the lower customers’ wish.
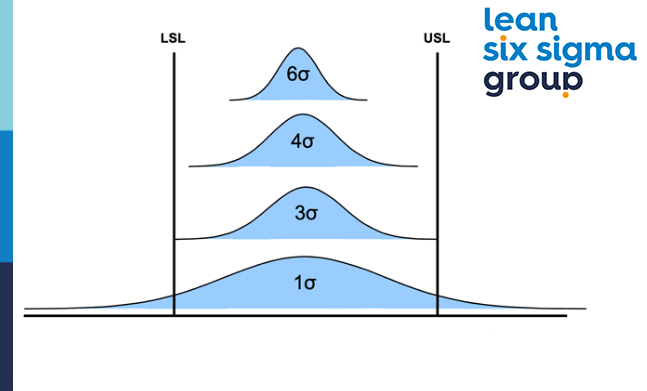
A process could be able to produce a nearly perfect outcome. The total performance of a process, from the customers’ perspective, can be 3,4 DPMO – this resembles a long-term performance with a value of 4,5 sigma. The difference between the ‘best state’, measured by taking the short-term process capacity, and the total customers’ experience (long-term) is also called Shift (Zshift of sshift). The shift of a classic process is 1,5. So when speaking of Six Sigma, this is inherent to the theorem which states that the short-term capacity of a process is 6 sigma and the long-term 4,5, using a standard deviation of 1.5. This is actually 3,4 DPMO from the customers’ perspective.
When referencing to the number of mistakes using DPMO, this often indicates long-term capacity of the process. Here, the experience of the customer is looked at. Key is the role of the Six Sigma professional: quantifying the performances of the process and choosing the right strategy to achieve the goal. If the value of Sigma increases from zero to six, the variation of the process decreases. When the value of the process reaches a certain level, the variation of the process will be around zero: ‘zero defects’.
Would you like to know more about this subject?
Is this indeed the case? Then do not hesitate and sign up for one of our Lean Six Sigma trainings!