Many organisations want to achieve an advantage by being better than their competitors. This is often done by making sure their processes are handled more efficiently, or in other words: cheaper. By lessening the costs and upgrading the quality of their products or services, organisations are able to consolidate their position in the market. And quite frequently, the processes to achieve such goals are filed under ‘Operational Excellence’. But what actually is Operational Excellence? And to which extent does the Lean philosophy fit in there?
What is Operational Excellence?
As just stated, Operational Excellence creates the opportunity for organisations to distinguish themselves from their competitors by excellerate in production processes. It originates from the model “CUstomer Intimacy and Other Value Disciplines”, which was first mentioned by Treacy and Wiersema in 1993. And not only did they create Operational Excellence, but they also defined two strategies which lets organisations become able to specialise in Product Leadership or Customer Intimacy.
Operational Excellence makes sure organisations strive towards a service where a customer’s wishes take on a central role within all processes. This means everything that is produced, is delivered when was asked and at the pre-arranged price. Why? Because this results in customer satisfaction. And when customers are content, employees of the organisation will most likely be more productive, because they become motivated. This will lead to a decrease of the total costs.
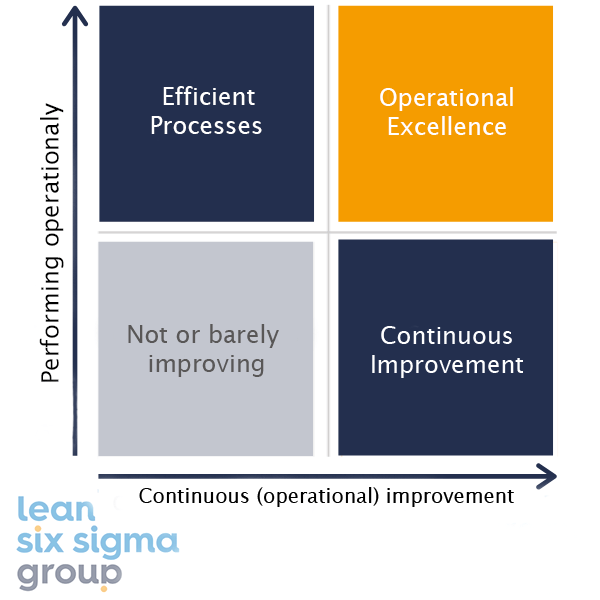
Features
To be able to fulfill the philosophy that is called Operational Excellence, many organisations invest in Supply Chain Management. This type of management strives for in-time stock and quick delivery of products. Because as you were just able to read, Operational Excellence focuses on the needs of the customer instead of those of the organisation.
A feature of Operational Excellence is an organisation being task-oriented. This means no unnecessary work is done and data is collected. Through analyzing this data, organisations can make sure their business processes become more efficient.
If organisations choose to apply this philosophy, they are able to gain a competitive advantage. How, you ask? It is actually rather simple. Because they will manage to offer their products/services at a lower price, considering they optimized their business processes, their profit increases.
But what about Lean and Operational Excellence?
As you may have noticed does Operational Excellence actually have quite some things in common with Lean (Six Sigma). This is why Lean is actually the most used methodology to achieve Operational Excellence.
If you are a little hesitant on why they have so much in common, this is a little overview. Both methodologies strive towards improving processes of an organisation. Both choose to do so by using a programmatic approach to be able to realise these process improvements structurally. And continuous improvement takes on a central role in both of these philosophies.
By focusing on customer value, process steps and eliminating non-added value activities, operational processes can be continuously improved which will eventually lead to Operational Excellence. Using the knowledge and qualities of your employees and effectively apply technology and innovation will lead to an increase of productivity, which is basically another word for process efficiency, and a much more reliable process (outcome).
The following Figure is a house, which is called the Lean house. This is a visualisation of the system which describes Lean: process improvement. It focuses on customer value and standardisation by striving for the best quality and littlest lead time to result in a more efficient process and eventually lower total costs.
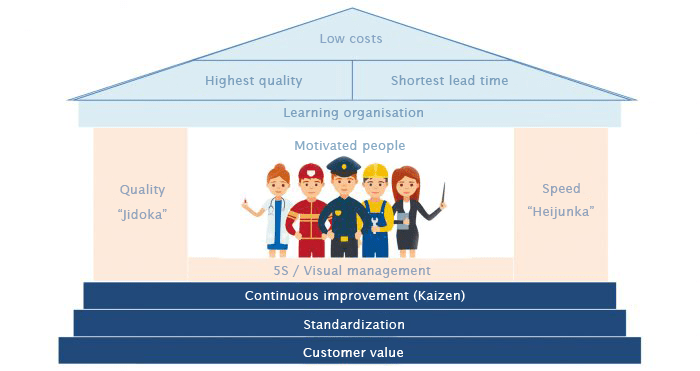
Operational Excellence is becoming more and more popular. But of course, if you want to apply this philosophy to your organisation, this will take more than just a snap of the fingers. It is important to make a change in behaviour. And not only does it take a long-term perspective to achieve these goals, it also requires perseverance. In other words, fully accepting, correctly applying and borrowing Operational Excellence within the entire organisation can actually take five to ten years.