Every company is unique. Of the many organisations that have embarked on the Lean Six Sigma adventure, some have achieved evident success, while it has not (yet) worked for others. Why did it work for some and not for others? Here, we share 8 lessons learned from successes and failures experienced in the launch of Lean Six Sigma.
1. Six Sigma must be integrated with Lean
Six Sigma techniques are effective in reducing process variation, but are not able to significantly improve process speed. Lean tools and techniques are specifically designed to reduce time wastage in processes. Today, a growing number of organisations are implementing Lean together with Six Sigma in order to achieve perfection in processes.
2. Lean Six Sigma efforts must support the objectives of the organisation
Successful implementations are based on a branded platform, i.e. essential change. Here, we have to consider aspects such as competitive advantage, gain or recovery of market share, introduction of new services, attracting new customers, retaining existing customers or a simple increase in profitability. Identifying a branded platform implies clarity among all managers on the reasons for the organisation’s implementation of Lean Six Sigma. It also means that decisions about the use of Lean Six Sigma are made on the basis of the question, “Will it harm our objectives or actually support them?”
3. All managers must be involved in the process
Managers will never fully back Lean Six Sigma if they consider it something that deprives them of resources, instead of a method that adds value and helps them achieve their goals. In order to avoid such pitfalls, an organisation must involve all managers in the start-up of a Lean Six Sigma project. By giving them a say when it comes to the selection of projects, prioritising and continuous monitoring, an organisation can count on their dedication.
4. Generate a selection of projects based on potential for value
If you were to ask your employees for improvement suggestions, you’d end up with more ideas than you could implement. The worst way of determining the best idea is by prioritising ideas submitted by senior management or ideas backed by the majority of management. The most effective Lean Six Sigma organisations run a strict selection of projects based on how much value a project can generate for shareholders.
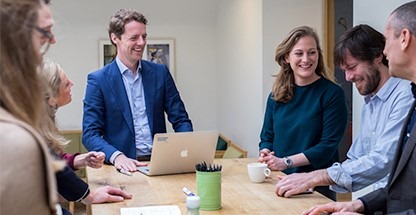
5. Find the critical mass of projects and resources
Some companies kick off their Lean Six Sigma implementation by training a handful of people and by launching a number of “trial” projects. Other organisations demand immediate dedication from the entire organisation and launch dozens of projects within the first six months. Both approaches are plausible, but a critical level applies to Lean Six Sigma efforts in every organisation. Once an organisation dips below that level, project progress and the required deteriorate. If the level is maintained, enthusiasm and dedication ensure lasting benefits.
6. Actively manage prospective projects
Given that most organisations want as many measurable and material results as possible within six months or a year, there is a tendency to push through as many Lean Six Sigma projects as possible. But one of the most important lessons learned from Lean principles is that too much forcefulness slows down a process and increases its runtime. As experienced Lean practitioners know, processes can be accelerated by reducing the amount of work demanded from every Black Belt. It is better to concentrate on rounding off a few important projects than to overrun the workplace with dozens of less-significant ones. Applying the right resources to the right projects ensures shorter runtimes.
7. Emphasise the importance of management skills
The use of Six Sigma requires a number of technical skills, such as an ability to process and analyse data. But good management skills are even more important. This emphasis on leadership is also relevant to how a company interprets the role of Black Belts. Giving Black Belt roles to people with strong management skills yields quick results and positive change within the organisation.
8. Vigorous tracing of results
Lean Six Sigma results must be quantified so that a company can correctly evaluate – and make decisions on – whether resources are being used wisely. At the very least, project runtimes and values must be regularly assessed in order to gain insight into any variation.
Ready to launch Lean Six Sigma at your organisation?
If you’d like to know more about applying Lean Six Sigma, you can book a Green Belt training or a Black Belt training.